Internal quality controls
We have put in place a number of procedures to meet customer requirements:
- Class I: standard application
- Class II: automotive / railway / high-volume / specific control applications
- Class III: safety parts – aerospace applications
These classes are different because of the customer’s specification and impact the coating processes (frequency and types of inspection – preparation – torque tests, etc.) and may generate a price variation.
For polyamide products (Tuflok – nylon HT)
- Torques tested during production do not require polymerization and validate production settings.
For microencapsulated products:
Torques are checked after polymerization (minimum 72 hours).
- Class I: by sampling on certain production runs
- Class II and III: systematically on all production runs, with results archived.
During these tests, we check torques according to customer standards (or DIN 267 part 27 if not specified).
We use a degreased raw steel nut (ISO4032) as standard.
We can use customer-specific tooling in certain cases.
Patch length, position and appearance are checked regularly.
We archive this data for traceability purposes.
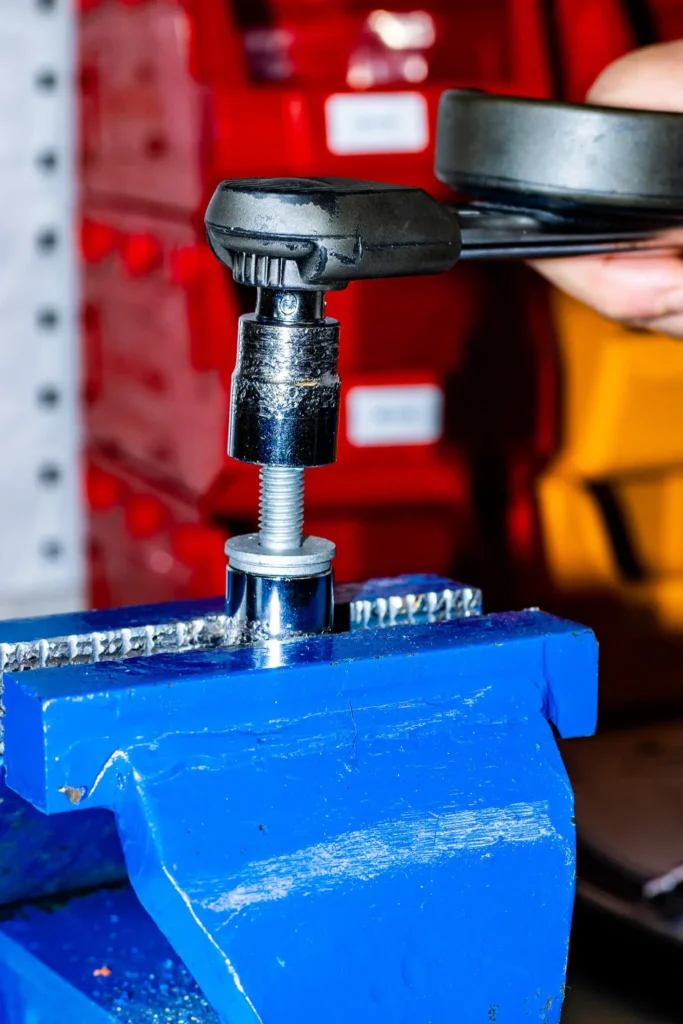
Standards and functions
Our wide range of products enables us to meet most standards, whether automotive, industrial, aerospace or railway.
We work closely with product suppliers to offer you the best technical solution for your application.
Each item to be coated is created with a reference standard to comply with.
In the absence of customer information, we use DIN 267 part 27 for microencapsulated products.
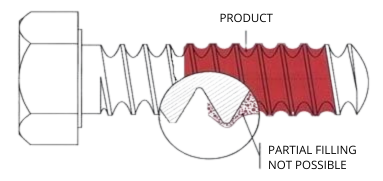
Coating length (LE) offered as standard:
LE: Value approaching 1 times the diameter (depending on pitch). Tolerance of +/- 1 thread
Example for an M8x125: LE= 8.75 mm (+/- 1.25) – i.e. 7 filled threads (+/-1 thread)
It is NOT possible to have an LE of 8mm on a pitch of 1.25, as the product will necessarily fill the entire thread, not just part of it.
Note: in case of doubt, it is necessary to have the feasibility of the position (PE) and length (LE) of the patches validated beforehand.
The Soprilok advantage
- Whatever class of procedure is chosen, our cameras or vision sensors control 100% of the coating on our machines.
- Our production runs are torque-controlled, and we track and archive torque-control results for statistical purposes. Take advantage of our experience to determine the best product to meet your application requirements.