What is Tuflok®?
Discover Tuflok®, the world’s most widely used polyamide locking product. Also known as “Nylon® Blue Patch” in Asia and America, this product is used for a multitude of applications, from caster screws to special aerospace fasteners.
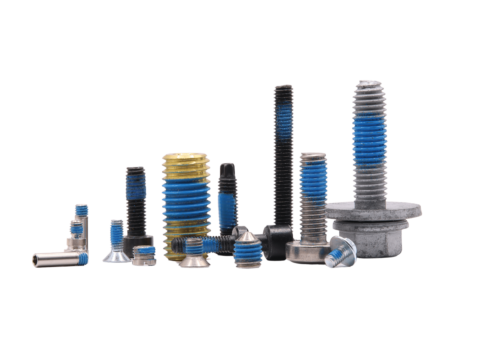
Why choose to apply Tuflok®?
Tuflok® is recommended for a variety of applications where adjustment during assembly or end use is required, such as set screws and temporary positioning. It is ideal for fasteners used in environments subject to constant vibration, offering a reliable solution for holding parts together. Its ability to resist shock and vibration makes it a preferred choice even in live assemblies.
In the electronics sector, it is essential for holding vibration-sensitive components in place, such as printed circuit boards in portable electronic devices.In construction, Tuflok is often used to secure structural elements subject to movement, such as solar panels or fences. Industrial equipment, such as machine tools and production equipment, also benefit from the use of Tuflok to ensure the stability of assemblies under intensive operating conditions.
The different versions of Tuflok®?
Tuflok® 180
Tuflok® 180 coating is applied to approximately 180° of the screw circumference. It is particularly recommended for adjustment screws.
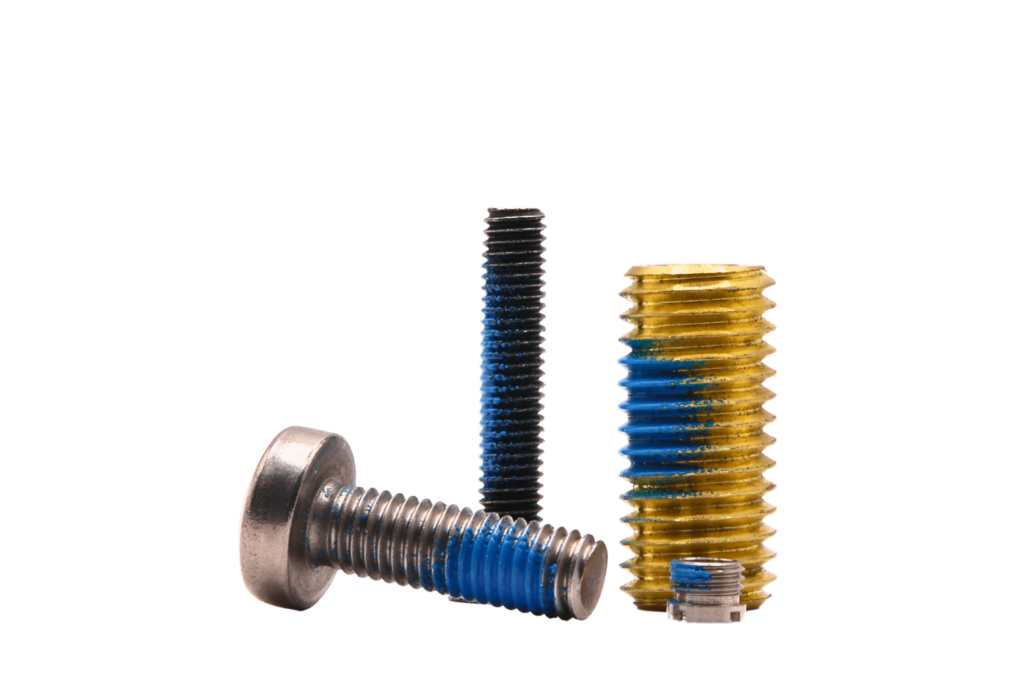
Tuflok® 360
Tuflok® 360 coating is applied around the entire circumference of the part. This product is ideal for applications requiring sealing against liquids or gases.
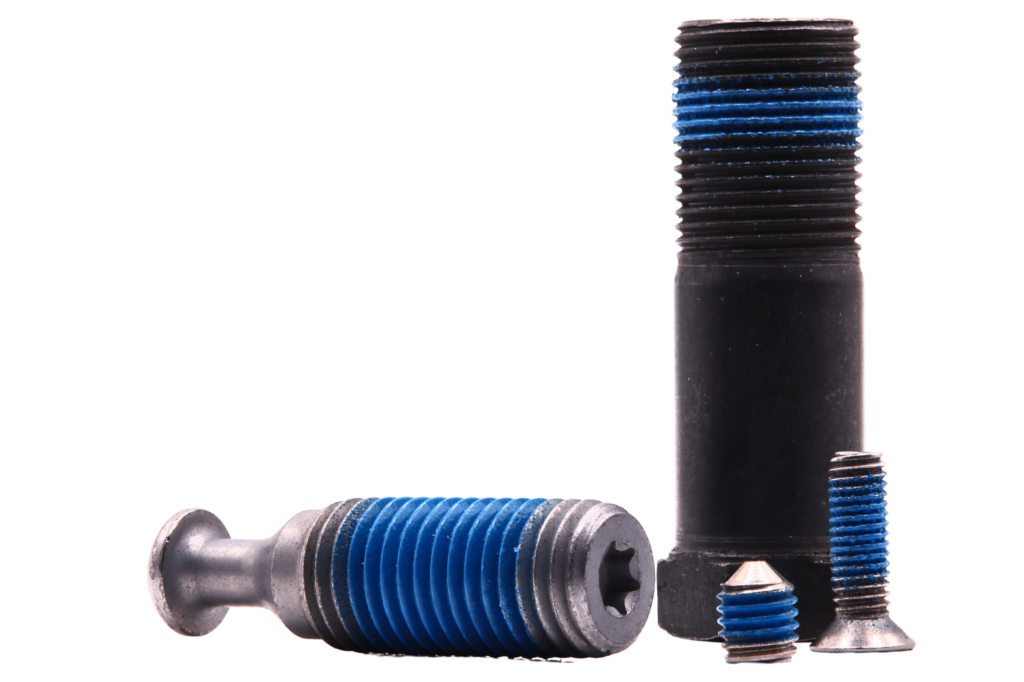
The advantages of Tuflok®
- Can be reused several times
- Good resistance to shock, vibration and chemicals
- Application can be precisely localized
- No polymerization: locking and sealing are immediate
- Operating temperature up to 120°C
- Locking with or without tension in the assembly
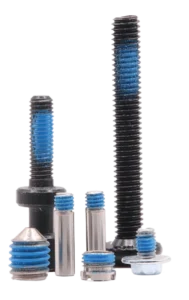
Torque performance
Reference standard: Stellantis: B14.12.35 LFM WITHOUT CLAMP LOAD
Diameter (mm) | 3 | 4 | 5 | 6 | 7 | 8 | 9 | 10 | 11 | 12 | 14 | 16 | 18 | |
Pitch (mm) | A | 0,5 | 0,7 | 0,8 | 1 | 1 | 1 | 1,25 | 1,25 | 1 | 1,25 | 1,5 | 1,5 | 1,5 |
B | 1,25 | 1,5 | 1,25 | 1,5 | 2 | 2 | 2,5 | |||||||
C | 1,5 | 1,75 | ||||||||||||
Cfv max. (N.m) | A | 0,2 | 0,5 | 1,0 | 1,7 | 2,7 | 4,1 | 5,8 | 8,0 | 11,0 | 14,2 | 22,4 | 33,9 | 48,7 |
B | 4 | 7,9 | 10,8 | 13,9 | 21,7 | 32,9 | 46,3 | |||||||
C | 10,6 | 13,6 | ||||||||||||
Cfd min. (N.m) | A | 0,04 | 0,1 | 0,2 | 0,3 | 0,5 | 0,8 | 1,2 | 1,6 | 2,3 | 2,9 | 4,6 | 7,0 | 10,1 |
B | 0,8 | 1,6 | 2,2 | 2,8 | 4,4 | 6,7 | 9,3 | |||||||
C | 2,1 | 2,7 |